
Replacing the nozzle and adjusting the electrodes on a Beckett oil burner. For example, Horizon Services in Delaware and Pennsylvania offers an $89 online special, while Seider Heating & Air Conditioning in Wisconsin charges $110 for a gas furnace or gas boiler and $180 for an oil furnace. (If simple parts like a nozzle or thermo coupler need replacing, it can add $50-$150 or more to the total.).
Residential and commercial oil-fired heating systems are generally serviced on an annual basis. During normal operation oil burner nozzles may accumulate sludge formations.These are not removed by fuel in the process of operating the burner but instead bake on nozzle walls. While the prevailing practice is to replace nozzles during servicing it may also be practical to recondition them in an ultrasonic cleaner.Cavitation action in an ultrasonic cleaner such as the available from iUltrasonic is an excellent way to remove built-up contaminants from nozzles. This unit has a cleaning solution capacity of 0.85 gallon (larger capacities are available) and operates at an ultrasonic frequency of 43 kHz. With a tank size of 9.38 x 5.38 x 4 inches deep the LR 610 ultrasonic cleaner is equipped with a heater, timer, drain and cover.A suggested cleaning solution is non-ammoniated biodegradable CLN-LR 110 concentrate, a natural solvent blend containing citrus oils and surfactants without toxic solvents or caustics.
This is shipped from iUltrasonic in 1 gallon containers. Recommended dilution is to 1 to 7 parts with water.Setting up the SystemOnce this system is in place you can clean a number of oil burner nozzles on an assembly line basis.Ultrasonic action can clean oil burner nozzlesWhen disassembled for cleaning fuel oil burner nozzles parts are quite small.
Therefore cleaning should be accomplished in separately ordered fine mesh baskets. Note: when disassembling the nozzles be careful not to damage the attached mesh strainers or sintered filters.Prepare a small batch of cleaning solution in a separate container such as the optional auxiliary pan.Load the parts in the fine mesh basket (do not overload) and pre-clean them by swishing them in the cleaning solution to remove excess fuel oil.
Allow them to drain. Note: The pre-cleaning solution should be discarded when it begins to look dirty. Dispose of it according to local regulations.Prepare the ultrasonic cleaning solution by filling the tank half full of water, then adding the correct amount of CLN-LR 110 concentrate based on the tank volume. Continue filling the tank.
Activate the cleaner for about 10 minutes to mix and degas the solution.When you are ready to clean set the thermostat to 130?F (54?C).Place the fine mesh parts basket in the separately ordered stainless steel cleaning basket and lower it into the cleaning solution. The basket keeps parts from contacting the bottom of the cleaning tank. Activate the ultrasound, set the timer for 20 minutes.During the cleaning cycle countless minute cavitation bubbles implode on contact with all fuel oil nozzle components to loosen and carry away contaminants.At the end of the cycle remove the parts, rinse with hot water, and dry.
They are now ready for reassembly.After repeated use the cleaning solution should be replaced. Drain the tank and as with the pre-cleaning solution, dispose of it in an approved manner.Call the iUltrasonic cleaning experts at 973-440-2191 for answers to your cleaning questions and recommendations on equipment sized to your requirements.
Oil Furnace Monthly Cost
Not all nozzles are exactly alike. There are variations from one manufacturer to another. Conversion charts are good guides, but they do not always take into account the variances.The problem is that standards do not exist to accurately define hollow and solid. Many methods have been proposed, but none perfected.This bulletin will provide you with several points to keep in mind when making for a burner retrofit job.THIS TASK HAS BEEN DONE FOR YOU IN APPLIANCE/BURNER PACKAGES. How Does It Work?Let’s look at how a nozzle works, and then consider what we expect a nozzle to do. Energy is required to break up the oil into droplets.
The energy is supplied by the fuel unit delivering oil to the nozzle from 100-150 PSIG for most residential applications and up to 300 PSIG for commercial applications. The nozzle, through the swirl slots, swirl chamber and orifice converts the energy from pressure to velocity. Approximately half of the pressure is converted or dropped across the swirl slots and chamber.At this point, as their name implies, the swirl slots cause the oil to swirl in the swirl chamber. The swirling oil is forced toward the orifice, causing the oil to form a hollow tube. As this hollow tube exits the orifice, a cone shaped film of oil develops.

The film quickly separates into ligaments (1) which stretch to their breaking point, thus forming the droplets.Refer to our, where the affects of viscosity on flow rate and droplet size were discussed. If you suspect that viscosity is causing a problem with combustion or light-off, do not hesitate to install a smaller nozzle and increase the pump pressure.
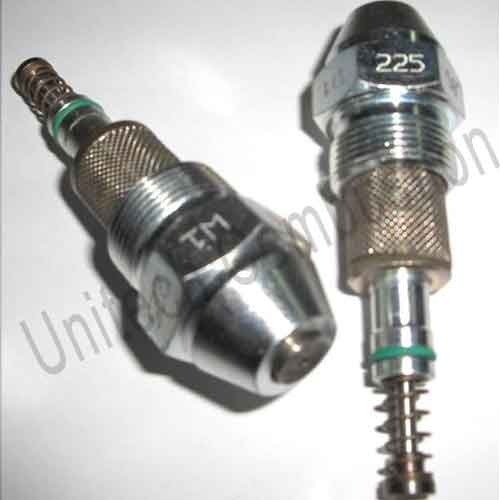
ExpectationsA nozzle is expected to deliver properly atomized fuel at a precise rate over a broad range of conditions. The fuel may be 40-50°F, the nozzle may operate at temperatures up to 250°F and the off cycle soak temperature may climb to nearly 300°F in some appliances.

In spite of the adverse conditions, we expect the nozzle to deliver properly atomized fuel at the correct rate, pattern and angle.We must help the nozzle do its job. First, make sure that the fuel supplied to it is clean and air free!
Make sure the pump pressure is set properly. For domestic applications it may be 100 PSIG to 150 PSIG. When installing the nozzle, use extreme care to protect the nozzle orifice and strainer. If the orifice gets dirt in it or becomes scratched, it will not function properly.Inspect the nozzle adapter before installing the nozzle. If there are deep grooves cut into it from previous nozzles, replace it. Those grooves or a scratched surface are a potential source for a leak.Do not over torque the nozzle when tightening.
Over torquing will cut grooves into the adapter and cause leaks when the next nozzle is installed. Hollow, Solid, All Purpose?Due to the lack of standards to define the qualities that we give a nozzle, it is difficult to even generalize about their use and application. In the laboratory many of the tests performed are conducted to select the proper nozzle. With any given combustion system, nozzle selection will be determined by the environment into which the burner is being placed.There are many choices available for a nozzle, it is best to follow the appliance manufacturer’s recommendations. They have, in conjunction with the burner manufacturer, conducted many tests to determine what works best.
Best Oil Furnace
What works best is that combination of components, including the nozzle, that meets the performance requirements of the appliance manufacturer, and results in smooth starts, runs and stops. At times this is a compromise. To obtain the proper light-off and run that is required for long-term cleanliness, some performance may have to be sacrificed. The nozzle that provides the highest level of performance in terms of CO₂ and smoke is not always the nozzle that provides the smoothest light-off and run. For those reasons we encourage following the manufacturer’s recommendations. Some GuidelinesWith our F series heads, we generally find that from.5 to 1.5 GPH, an 80° hollow works best. For all of the reasons noted above, however, that is not a hard and fast rule.
There are some O.E.M. Applications that call for solid nozzles in this range.From one gallon and up, our typical application is running with an 80° solid. Yes, there is an overlap between a gallon and a gallon and a half. The only sure way to know which nozzle provides the best performance is to put them in and run the combustion tests. That is the way the correct nozzle is determined in the laboratory.Here are some other factors. The burner combustion system is a factor as is the chamber size and shape. Over the years, correlations have been drawn between “burner air patterns” and nozzle and chamber configuration and nozzle pattern.
With today’s flame retention burner, these generalities no longer hold true.The circulation or recirculation patterns within the combustion zone and the design of the burner combustion parts will have a much greater influence than any of the other factors involved. The flow of gases within the combustion zone is extremely difficult to study without disturbing or upsetting the pattern.
Therefore, when you must install the nozzle, test it with instruments, listen to it and look at the flame for the best performance possible. Nozzle SizingMuch information is available regarding the selection of the proper nozzle size in a retrofit application. We cannot cover it all here. Instead, the sources of that information are listed below.
Guidelines for combustion chamber size for a given firing rate are provided by the burner manufacturers for retrofit applications. This information is found in the installation instructions manual. Remember, the proper nozzle size has already been selected for you in the case of a package unit. ConclusionWhen considering proper nozzle selection, remember these points:. Always use the appliance manufacturer’s nozzle specifications. Follow the burner manufacturer’s recommendations when retrofitting a new burner to an old appliance.
You must set-up the combustion with properly maintained test instruments. Smoke, CO₂, or O₂, drafts and pump pressure. Once the CO₂ has been determined at a trace of smoke, add enough extra air to reduce the CO₂ one and one-half percent.INFORMATION SOURCESNozzle SizingR.W. Beckett Corporation, P.O. Box 1289, Elyria, OH 44036“ Heat Loss Calculation Guide,” The Hydronics Institute,35 Russo Place, Berkeley Heights, NJ 07922“ Cooling & Heating Load Calculation Manual,” American Society of Heating, Refrigeration and Air Conditioning Engineering, Inc.
(ASHRAE),1791 Tullie Circle, N.E., Atlanta, GA 30329How Does It Work?“ A Total Look at Oil Burner Nozzles,” Delavan Manufacturing,West Des Moines, IA 50265 FOOTNOTE(1) Delavan Manufacturing, Spray Droplet Technology, ©1973 Post navigation.
